На уникальные проекты новичков не берут
Надежность высотных сооружений во многом зависит от того, как был организован строительный контроль на площадке. Качество строительства МФК «Лахта-центр», наряду с другими организациями, контролирует компания AECOM. О специфических задачах, которые приходится при этом решать, рассказывает руководитель проекта AECOM Алексей Сынчиков.
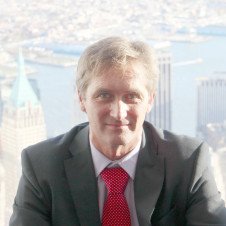
Сынчиков Алексей
AECOM
– У AECOM значительный опыт работы с небоскребами. Какие известные высотки есть в международном портфеле компании?
– AECOM участвовал в реализации более 500 высотных проектов по всему миру. Среди них – Всемирный торговый центр в Нью-Йорке, The Shard в Лондоне, Бурдж-Халифа в Дубае. Кроме строительства МФК «Лахта-центр», сейчас команда AECOM работает на проекте «Абу-Даби Плаза» в Астане. Предполагается, что это будет самое высокое здание в Центральной Азии. В Москве компания участвовала в строительстве многофункционального терминального комплекса ММДЦ «Москва-Сити», в который войдут здания высотой до 170 м и транспортный терминал, обеспечивающий пешеходную связь между МMДЦ, метрополитеном и городским транспортно-пересадочным узлом.
– А как компания пришла на самый северный небоскреб мира?
– С нашим заказчиком мы познакомились в 2007 году, когда башню «Охта-центра» планировали строить возле Большеохтинского моста. Тогда AECOM выиграл тендер на управление строительством. Проект был приостановлен, но хорошие отношения с заказчиком остались. И когда в 2011-м было принято решение о строительстве МФК «Лахта-центр», заказчик пригласил нас для контроля за инженерно-геологическими изысканиями, а также для консультаций по проектированию подземной части комплекса. Тогда на проекте работали всего пять человек из АЕСОМ. Однако по ходу его реализации менялись задачи и объем работ. Сейчас компания силами 50 сотрудников осуществляет контроль за строительством всего комплекса.
– AECOM справляется силами российской команды? Или на этот проект пришлось привлечь коллег из других стран, где опыт высотного строительства больше?
– Сейчас на площадке работает чисто российская команда. В этом нет никакой политики. Команда формируется исходя из задач, которые ставит заказчик. Поскольку речь идет о строительном контроле, который базируется на российских строительных нормах, нам необходимы инженеры, знающие отечественную нормативную базу.
На этот проект компания направляет проверенных сотрудников. Если их не хватает, мы ищем специалистов на открытом рынке. Высшее образование и опыт работы имеют ключевое значение. AECOM охотно сотрудничает с молодыми специалистами, но на такой проект, как «Лахта-центр», новичков, конечно, не берут. Строительный контроль для инженера – это большой объем самостоятельной работы, когда от ошибок страхуют не коллеги, а квалификация. Ведь если он принял работу, не заметив дефекта, это отразится на качестве, а значит, на имидже компании. Мы должны доверять специалисту.
Например, Михаил Скугарев, один из наших инженеров-электриков долго ходил в море, отвечал за все энергосистемы судна во время плавания. Мы приняли это во внимание, хотя в первую очередь, конечно, учитывали его опыт работы на стройке после списания на берег. Владимир Караулов прошел все ступени строительства, начиная с проектирования электрических систем и заканчивая их эксплуатацией. Он способен не только сверить фактически выполненную работу с проектом, но и оценить проектное решение и дать рекомендации по выбору оборудования.
Для работы с фасадами мы искали специалистов, знакомых как с модульной фасадной системой, которая монтируется на башне компанией Gartner, так и с системами структурного, спайдерного или стоечно-ригельного остекления, которые наряду с модульной системой будут установлены на многофункциональном здании «Лахта-центра». Человек, освоивший только стоечно-ригельную систему и не знакомый с модульной, возможно, и справился бы. Но это риски.
Сейчас на объект выведены практически все строители, механики, электрики, слаботочники, специалисты по фасадным системам. График работы подразумевает, что строительный контроль идет семь дней в неделю 24 часа в сутки, с учетом работы в праздники и выходные. Кстати, разработкой и оптимизацией проектных решений для «Лахта-центра», а также стратегией строительства занимается компания Samsung, о специалистах которой я могу сказать много лестных слов.
– Когда здание строится не по СНиПам, а по специальным техническим условиям, насколько это усложняет строительный контроль?
– Проблема в том, чтобы технические условия были выпущены в принципе. Если они есть, то все в порядке. Заказчик уделял этому особое внимание еще на этапе проектирования. Поскольку АЕСОМ имеет опыт в проектировании и управлении строительством высотных объектов, наши специалисты вместе с заказчиком и проектировщиками участвуют в разработке технических условий, техрегламентов, проектов производства работ. Командная работа позволяет создать понятную схему контроля и приемки работ.
Безусловно, нестандартные задачи и вопросы возникают постоянно. Иногда ответ можно найти только экспериментальным путем. Иногда мы используем международные резервы АЕСОМ. Например, с офисом в Нью-Йорке мы обсуждали монтаж наклонных стальных колонн. У башни «Лахта-центра» – наклонные колонны и фасад, поворачивающийся на один градус на каждом этаже. Башня закручивается. Как контролировать в этом случае качество монтажа? На этот вопрос важно ответить, пока готовится и утверждается проект производства работ.
Для американских коллег поиск решения был не менее интересен, чем для нас. Большинство высоток в Нью-Йорке сделаны совершенно стандартно, с использованием простой конструкции: бетонное ядро и металлические балки. Все это пройдено множество раз. В Дубае есть закручивающаяся башня Infinity, но без «падающих» колонн. Надо признать, что «Лахта-центр» набрал максимально возможный уровень сложности, какой существует в мире на данный момент.
- Опыт строительства подземной части комплекса уже изучается на научно практических конференциях. Какую роль сыграл в этом AECOM?
– Я бы не стал выделять роль одной компании. Подземная часть «Лахта-центра» действительно обладает уникальными характеристиками, но над ней трудилась целая команда. Кроме того, привлекались ведущие НИИ, работа сопровождалась большой программой испытаний. Перед тем как утвердить тот или иной технологический регламент, проводились натурные эксперименты.
Начнем с того, что для исследований грунтового массива в ходе инженерно-геологических изысканий пришлось приобрести специальное оборудование, которого не было в России. НИИОСП им. Н.М. Герсеванова разработал специальную методику для оценки несущей способности грунтов при давлении, которое будет оказывать башня. Напомню, высота здания – 462 м, а расчетная нагрузка на основание составляет 670 000 тонн. Чтобы спроектировать и построить надежный фундамент, грунты, залегающие в основании, пришлось исследовать до глубины 120 м. Действующие российские нормы установлены для значительно меньших глубин и рассчитаны на меньшее давление.
Далее пришлось провести натурные испытания, чтобы определить несущую способность свай. Устройство свай приходилось вести с поверхности, что увеличивало их длину до 72 и 82 м. Мы испытали по две сваи каждой длины диаметром 2 м по методу Остерберга. Я не знаю другого объекта, на котором были бы проведены аналогичные испытания на таких глубинах.
Устройство сухого котлована глубиной 21 м в 40 м от Финского залива, единовременное бетонирование фундаментной плиты высотой 3,6 м и объемом почти 20 000 «кубов» – все это представляет немалый интерес для специалистов. Это результат почти двухлетней работы проектировщиков и технологов. Для разработки составов бетона были привлечены НИИЖБ им. Гвоздева (Москва) и НИИ гидротехники имени Б.Е. Веденеева (Петербург). Были обследованы более двадцати бетонных заводов, из которых выбрали 13. Они смогли обеспечить необходимую стабильность поставок и качество бетона. Характеристики самоуплотняющихся бетонных смесей проверяли сначала в лабораториях, а затем на опытных участках.
Весь процесс заливки фундаментной плиты был «отрепетирован» на опытном образце: измеряли температуру смеси, расплыв, время живучести бетона, скорость схватывания и множество других показателей. Специалисты должны были убедиться, что конструкция получается без рабочих холодных швов. Только после подтверждения всех расчетных параметров было принято решение о бетонировании фундаментной плиты. AECOM внес посильный вклад в эту работу.
– Уже известно, что на фасаде башни нет двух одинаковых элементов. Как в этом случае контролировать их качество?
– Если нет одинаковых элементов, при монтаже обычно используют штрих-код, который наносится на изделие. Он считывается специальным устройством, которое показывает, куда этот элемент должен встать. Если панель не встанет в назначенное ей место, ее придется переделывать. Пока такого не было. Фасады башни изготавливаются на заводе Gartner, где перед отправкой обязательно делают контрольную сборку.
Что касается монтажа, после того как собраны два этажа, процесс более или менее отлажен. Мы должны проследить за качеством монтажа, обеспечить герметизацию фасада. Он должен соответствовать требованиям к ограждающим конструкциям в наших климатических условиях. И конечно, нужно реализовать замысел архитекторов и заказчика.
– Специалисты говорят, что многофункциональное здание по сложности не уступает башне.
– Это правда. Например, у здания спроектированы наклонные торцевые фасады, консоль которых в некоторых местах достигает 21 м. На двух блоках здания, начиная с пятого этажа, все этажи «вывешиваются» на железобетонных ядрах. Это позволяет создать огромное открытое пространство внутри. Достигается эффект за счет специально спроектированных ферм. Качество изготовления и точность монтажа металлоконструкций играют здесь первостепенную роль.
Важно упомянуть еще об одной проблеме, которую решали с помощью ЦНИИСК имени В.А. Кучеренко. Для «Лахта-центра» пришлось разработать особый регламент сварных соединений. Он применяется при сварке узлов ферм, которые изготавливают из сталей толщиной до 100 мм. Наши нормы не дают ответа, при каких режимах это возможно сделать без потери качества, какие проходки нужны, с каким перерывом. Надо было оценить, как влияет нагревание при сварке на изготавливаемый шов и соседние швы, прежде чем выпустить регламент. А впереди – монтаж арки с пролетом почти 100 м, в ходе которого придется также учитывать жесткие температурные требования. Арку надо замкнуть наверху так, чтобы конструкции не разрушились ни в процессе работ, ни потом. Все это сложно, но безумно интересно.