Ольга Дорофеева: «Из панелей можно строить дома с любыми планировками»
В строительной корпорации «ЛенРусСтрой» стараются диверсифицировать бизнес. В ее состав входят полтора десятка компаний разного профиля – от проектирования и строительства до благоустройства. Есть даже собственное сельскохозяйственное производство, как шутит основатель и глава корпорации Леонид Кваснюк, – «на черный день». Однако и оно уже приносит прибыль. Имеется и свой домостроительный комбинат – Киришский ДСК. Об истории модернизации предприятия более чем с полувековой историей и об уходе от «серий» в панельном домостроении рассказывает его генеральный директор Ольга Дорофеева.
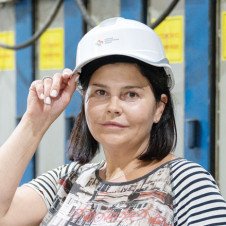
Дорофеева Ольга
— Зачем понадобилась модернизация ДСК и когда она началась?
— К моменту интегрирования комбината в наш холдинг предприятие уже было неконкурентоспособным. Не было гибкости в плане номенклатуры изделий. Например, чтобы перейти на производство железобетонных изделий другой серии, надо было вручную переделывать металлические формы, а это трудоемкий и дорогостоящий процесс, который занимает до двух месяцев. Нужно было увеличить скорость переналадки, а также повысить качество изделий. Оно уже не соответствовало требованиям заказчиков.
Сначала модернизация была пошаговой: чтобы полностью «переобуться», нужны были миллиарды. Нам предстояла не только модернизация, но и реконструкция. Ливневая, дренажная системы, кровля и фасады цехов – все подлежало замене. Вкладываться надо было не только в оборудование, но и в сами здания и сооружения.
В первую очередь мы поменяли фасады, поставили новые окна, устранили все течи и зазоры в стыках. До этого в цехах было очень холодно и люди работали в ватниках. За два года заменили все осветительные приборы. Вроде бы несложно, а на самом деле – большая работа. Результат тоже ощутимый: в первый же год только на электроэнергии сэкономили около 5-7 млн рублей.
В 2019 году, когда здания цехов были полностью подготовлены для нового оборудования, а предприятие роздало часть долгов, мы купили новую производственную линию. Затем приобрели четыре поворотных стола и итальянскую кассету вертикального формования. По чуть-чуть сделано очень много. Например, заменены почти все старые бетономешалки, проведена ревизия кранового хозяйства (два крана перевели на управление снизу), выполнен капитальный ремонт нескольких козловых кранов, обновлены силосы для цемента и т.д.
Сейчас мы своими силами собираем с нуля еще одну универсальную производственную линию, необходимую для увеличения объемов производства. На этих новых вибро-столах можно сделать почти любые панели и детали домов, а также повысить их качественные и конструктивные характеристики. Новая линия позволит значительно увеличить объёмы выпускаемых изделий.
Когда-то на предприятии было 370 сотрудников, но из-за старого оборудования и высокой трудоемкости объем выпуска был таким, как сейчас, или даже меньше. Сегодня мы производим изделия для строительства 70 тыс. кв.м жилья в год. И это всего около 240 сотрудников. Причем мы можем вдвое нарастить объем, не нанимая новый персонал.
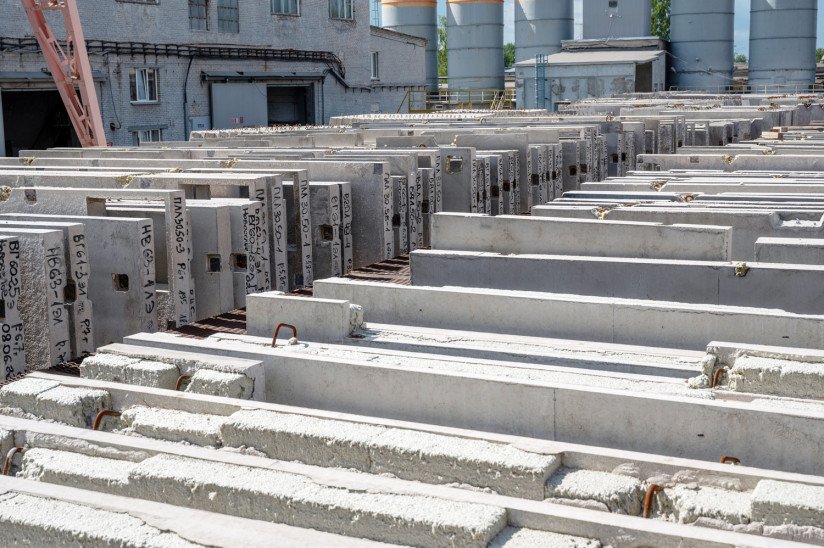
— Вы говорили про разнообразие номенклатуры. Речь о домах нескольких серий?
— Новое оборудование позволит выпускать индивидуальные домокомплекты. Из панелей можно собирать дома с любой квартирографией и многообразием планировочных решений. К «панельным сериям» мы больше не привязаны и готовы реализовать любые фантазии архитектора и проектировщика. На самом деле, наш ДСК серийных домов не делает давно. С 2016 по 2022 годы мы выпустили всего лишь три одинаковых домокомплекта, а все остальные кардинально отличались друг от друга.
— Продукция нужна самой корпорации или вы планируете продавать панели на внешнем рынке?
— Такие планы всегда были и остались. С 2016 года мы выполнили два сторонних заказа, причем один из них очень сложный с точки зрения технологии. Мы открыты для сотрудничества.
— Вы можете производить полные домокомплекты, или что-то заказчику придется докупать?
— Тут все зависит от его желания. Некоторые компании, например, возводят панельные дома, но с монолитными перекрытиями. Мы же готовы поставить весь набор железобетонных изделий, необходимых для сборки дома. В том числе преднапряженные плиты для большепролетных перекрытий. Освоен также выпуск трехслойных стеновых панелей для коммерческих помещений с высотой 4,3 м. Раньше их отсутствие было большой проблемой для застройщиков. Первые этажи приходилось лить из монолита, поскольку коммерческим помещениям нужны высокие потолки.
— Как планируете развиваться дальше?
— Есть много возможностей. То, что раньше считалось фантастикой, уже стало реальностью. Например, уже производятся целые железобетонные модули площадью до 100 кв.м. Фактически это готовые комнаты или даже квартиры, которые монтируются на стройплощадке, как кубики конструктора. Я когда-то мечтала об автоматическом станке для гибки арматуры, а сейчас он уже работает. Скоро мы установим станок, который будет изготавливать каркасы для армирования панелей. Почему бы не помечтать о производстве таких модулей? С их помощью мы получим уже не быстровозводимые здания, а сверхскоростное строительство.
Модернизация – процесс вечный, он никогда не прекращается, как ремонт в квартире. Например, всегда нужно, что-то обновлять, улучшать и приобретать.
Мы хотим развиваться и наряду с модернизацией постоянно учимся, растим новые кадры, повышаем их квалификацию. Мы можем работать как на сторонних, так и на внутренних заказчиков.
— Спрос на панель есть?
— Есть. Ведь этот способ строительства очень технологичен. Но в свое время в наш регион завезли финские технологии производства панелей, пролоббировали их, а теперь эти компании с рынка ушли. В результате утрачена очень мощная местная конструкторская база. Инженеров, которые могут работать с панелями, создавая при этом современные проекты, мало. Всех подсадили на импортные технологии. А те, кстати, оказались не такими уж рентабельными. Мы часто объясняем заказчикам, что на кубический метр «финского» изделия, например, заложено 85 кг арматуры, а мы можем сделать деталь той же прочности, использовав всего 47 кг арматуры. В одном из проектов мы подсчитали, что на четырех парадных только на арматуре экономия составит 40 млн рублей.
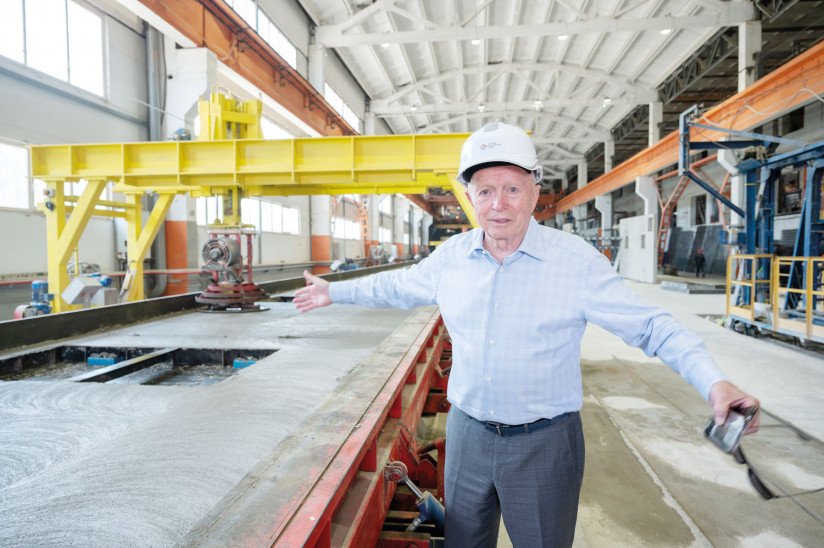
«С панельным домостроением связано очень много стереотипов. Например, многие вспоминают жуткие швы, которые приходилось постоянно герметизировать, потому что они протекали, и из них дуло. Мы теперь делаем панели, которые стыкуются практически без швов. В домах – «мокрые фасады», внутри все оштукатурено. Вы никогда и не узнаете, что это панельный дом, а не монолитный.
Еще одно неприятное воспоминание – низкие потолки. Но в наших панельных домах их высота – 2,7 м. Звукоизоляция в монолитных домах нисколько не лучше, а зачастую и хуже, чем в наших «панельках». Кроме того, при строительстве монолитных домов бетоносмесительные узлы на стройплощадке зачастую обслуживает пара гастарбайтеров. Там нет технолога, нет лаборатории, нет ОТК. Качество бетона, привезенного сторонним подрядчиком, тоже далеко не все проверяют, да и сложно это на стройке сделать. Есть примеры, когда привозной бетон так и не набирал прочность, и конструкции приходилось разбирать. Это колоссальная работа. У нас лаборатория работает ежедневно, регулярно берутся керны для проверки, каждое изделие паспорт имеет. Да и создаются панели в «тепличных» условиях, а не на улице в мороз или дождь.
Кроме того, панельный дом строится вдвое быстрее, что особенно важно теперь, когда все застройщики «сидят» на эскроу-счетах, и не могут получить с них деньги, пока дом не введут.
Так что теперь наша задача – загрузить комбинат на полную мощность, показать возможности ДСК, найти сторонних заказчиков, а потом покупатели сами будут за этими панелями бегать. Панельное домостроение обходится дешевле и делается быстрее. Мы готовы это доказывать на конкретных цифрах. »
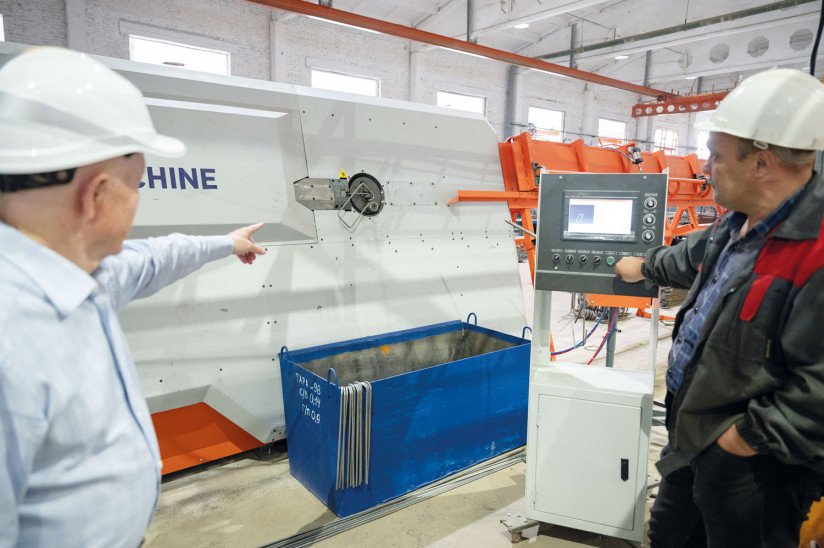
ДОСЬЕ «НП»
- Киришский ДСК основан в 1969 году как преемник завода железобетонных изделий, открытого в 1964 году для строительства города Кириши.
- ДСК сотрудничал с «ЛенРусСтроем» с 2005 года, а официально вошел в состав корпорации в 2016 году.
- Предприятие занимает 11 га, на которых размещены производственный корпус на семь технологических пролетов со встроенным бетоносмесительным оборудованием, корпус с технологической газовой котельной, корпус под перспективное производство.
- Среди оборудования – универсальная производственная линия, поворотные столы, кассеты вертикального формования, колонно-ригельная линия, линия для производства преднапряженных плит перекрытий.
- ДСК производит наружные трехслойные и внутренние стеновые панели, вентиляционные блоки, сборные лифтовые шахты, лестничные марши и площадки, плиты перекрытий, цокольные панели, панели сборного парапета, колонны, ригели, преднапряженные плиты перекрытий, блоки фундамента и т.д.
Материал подготовлен в рамках специального проекта NSP.RU - "ДОСТИЖЕНИЯ ГОДА", приуроченного к профессиональному празднику День строителя.